Industrial Equipment Paint Services: Essential for Longevity and Performance
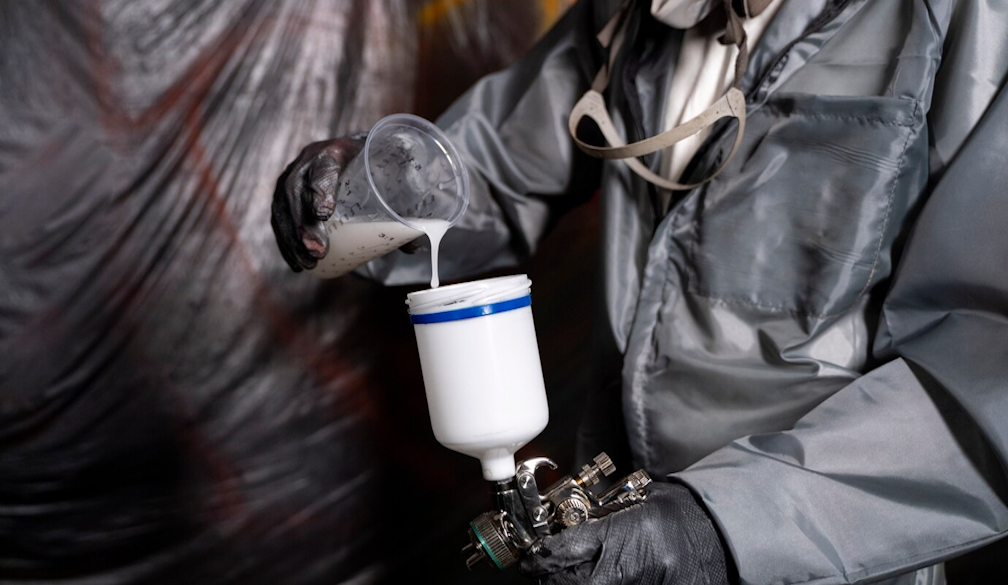
In the world of heavy machinery and industrial operations, the paint job on equipment might seem like an afterthought. However, industrial equipment paint services are critical to the functionality, durability, and appearance of machinery that operates in some of the harshest conditions imaginable. Industrial equipment, from cranes and forklifts to complex manufacturing machinery, faces constant exposure to wear and tear, extreme weather, and corrosive materials. Industrial equipment paint services are not just about enhancing the visual appeal of machinery, but also about ensuring that it operates efficiently for years to come.
The Role of Paint in Industrial Equipment Maintenance
It acts as a protective barrier between the machinery and the environment, ensuring that the equipment can handle the stresses it faces day in and day out.
- Corrosion and Rust: When equipment made of steel or iron is exposed to moisture and oxygen, oxidation can cause it to rust. Corrosion weakens the metal and compromises the integrity of the machine. High-quality industrial paint acts as a barrier to prevent water and air from making contact with the surface, helping to extend the lifespan of the equipment.
- Abrasion and Wear: Industrial equipment is often exposed to harsh conditions, such as high-impact materials, dirt, and chemicals. The constant abrasion can wear down the surface, leading to exposed metal and potential failure. A durable coating prevents direct contact between the machinery and the damaging elements, protecting the integrity of the equipment.
- UV Radiation: Prolonged exposure to sunlight can lead to fading and degradation of the paint itself, especially in outdoor equipment. UV radiation breaks down the molecular structure of paint, causing it to crack, peel, and lose its protective properties.
- Chemical Exposure: Some industries, like construction or manufacturing, involve the use of harsh chemicals that can corrode or degrade machinery. Industrial paint coatings that are resistant to chemicals help protect machinery and prevent expensive damage.
Types of Coatings for Industrial Equipment
Choosing the right type of coating is essential for ensuring that the equipment is protected against the specific challenges it faces. Here are some of the most commonly used coatings in industrial painting services:
Epoxy Coatings
Epoxy coatings are one of the most popular choices for industrial equipment because of their durability and resistance to chemicals and abrasion. They form a strong, long-lasting bond with metal surfaces, providing excellent protection against rust and corrosion.
Polyurethane Coatings
Polyurethane coatings are known for their superior flexibility and UV resistance. This makes them an ideal choice for equipment that is exposed to outdoor conditions or variable temperatures. Polyurethane coatings are often used for machinery that undergoes frequent movement or vibration, as they can withstand these stresses without cracking or peeling.
Acrylic Coatings
Acrylic coatings are often used when a smooth, glossy finish is desired. While they may not offer the same level of protection as epoxy or polyurethane, they are still highly resistant to UV rays, weathering, and fading. Acrylic coatings are commonly used on machinery where appearance is important, but they can also be used in less demanding environments where chemical resistance isn’t a primary concern.
Zinc-Rich Coatings
Zinc-rich coatings are primarily used for their corrosion resistance. The high zinc content in the coating helps prevent rust by providing a sacrificial layer that corrodes in place of the underlying metal. These coatings are particularly useful in high-humidity or marine environments where rust is a significant concern.
Ceramic Coatings
Ceramic coatings are often used for high-temperature industrial applications, such as turbines, exhaust systems, and furnaces. These coatings offer excellent thermal resistance and can withstand extreme heat, making them ideal for components that are exposed to high temperatures.
The Process of Industrial Equipment Painting
Industrial equipment painting is not a simple task—it requires careful planning, preparation, and skilled execution to achieve a long-lasting, high-quality finish.
Surface Preparation
Before any paint is applied, the equipment must be thoroughly cleaned and prepared. This includes removing dirt, grease, oil, rust, and old paint. Surface preparation can be achieved through sandblasting, power washing, or chemical cleaning.
Priming
Priming is an important step that helps improve adhesion between the surface and the paint. A primer is applied to create a bonding layer that enhances the durability and corrosion resistance of the paint job. The type of primer used depends on the equipment material and the conditions it will be exposed to.
Application of Topcoat
Once the primer has dried, the topcoat is applied. This is where the chosen coating material (epoxy, polyurethane, etc.) is sprayed, rolled, or brushed onto the equipment. The application method depends on the type of equipment and the desired finish.
Curing and Drying
After the topcoat is applied, it must be cured and dried to ensure the coating hardens properly. This process can take several hours or even days, depending on the type of paint used and the environmental conditions. Some coatings require heat to cure, while others dry naturally at room temperature.
Inspection and Touch-ups
Once the paint has dried, the equipment is carefully inspected for any defects or imperfections. Any touch-ups or additional coats needed are applied to ensure the paint job is smooth, even, and free of defects.
Final Thoughts
Industrial equipment paint services are more than just a cosmetic upgrade; they are an essential aspect of maintaining and protecting valuable machinery. By using the right coatings and applying them with precision, businesses can ensure their equipment remains functional, safe, and visually appealing for years to come. Whether protecting against corrosion, improving safety, or enhancing the overall appearance of machinery, industrial painting services are a worthwhile investment that helps companies maintain their assets and improve their bottom line.